1顶棚结构分析
顶棚结构如图1所示,尺寸约2 224 mm×1 227 mm,质量为14.288 kg,厚度为0.7 mm,材料牌号为JAC340P-45/45。由于车辆外观造型的需求,两外侧翻边整形为点焊焊接边,翻边面与A级外观面存在5°的夹角。顶棚具有尺寸大、拉深深度浅、造型简单等特点,因此为了减少模具工序、提高工序的集成度,将其两侧和尾部修边、翻边及整形工序集成,现以零件两侧流水槽的模具结构为对象进行说明。
图1 顶 棚
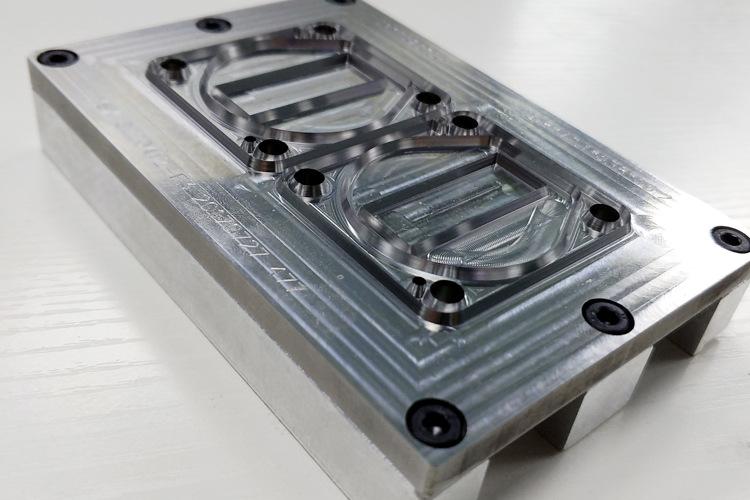
2原模具结构方案及疲劳寿命模拟分析
2.1 原模具结构方案
零件两侧流水槽采用2工序的成形方案。第1工序为拉深成形零件大致形状;第2工序为斜楔修边翻边整形完成零件两侧流水槽的成形。
第1工序模具如图2所示,该拉深模采用单动拉深方式成形零件大致形状。第2工序模具如图3所示,活动凸模2、修边翻边整形斜楔4、固定凸模5与压料板6完成顶棚两侧的修边翻边整形工序,修边翻边整形斜楔4工作时的侧向力传递到斜楔滑块3,斜楔滑块3采用桥架结构,便于修边废料顺利滑出模具,模具结构紧凑,实现了修边、翻边和整形工序的集成。下模座采用桥架结构,如图4所示,桥架结构应力较为集中,在高强度循环工作环境下,下模座存在失效风险。
图2 第1工序模具结构
1.凸模 2.压边圈 3.凹模
图3 第2工序模具结构
1.下模座 2.活动凸模 3.斜楔滑块 4.修边翻边整形斜楔 5.固定凸模 6.压料板
图4 下模座结构
2.2 疲劳寿命数值模拟分析
对于车身覆盖件模具,模座材料一般采用灰铁铸件,常采用的材料为HT300,其材料力学性能如表1所示。
表1 HT300材料力学性能
模具零件属于高周疲劳,因此采用S-N曲线法进行全寿命的疲劳分析,根据材料的力学性能参数,利用Ncode-designlife软件的SNAnalysis模块可获得HT300的S-N曲线[5]为y=236.908-15.683ln(x+78.288),如图5所示。
图5 HT300的S-N曲线
为了验证模拟分析结果的可靠性,首先对下模座进行应力状态及疲劳寿命的有限元分析,然后与实际生产的模具进行对比。为了保证有限元的速度和精度,采用自适应网格划分。根据对模具结构受力状态进行分析,下模座反侧受力P=408.1 kN,整个下模座为固定约束状态。
下模座应力分布云图如图6所示,桥架处的等效应力最大,说明该处应力集中明显,模拟得出等效应力为19.5 MPa,小于HT300的极限强度和屈服强度,下模座在工作时是安全的。寿命模拟分析结果如图7所示,桥架处的疲劳寿命最短,为40.2万冲次,但该顶棚模具设计需求寿命为100万冲次,因此该模具结构方案不满足要求。模具采用3工序成形方案,零件两侧顶棚搭接处仅前2道工序就完成成形,第1工序拉深,第2工序集成了修边、翻边和整形。模具结构复杂,布局会受到限制,为了使修边废料能够顺利滑出,模具只能采用桥架结构。
图6 应力分布云图
图7 寿命模拟分析结果
模具生产40~50万件后,第2工序的桥架结构二级废料刀座面拐角处出现裂纹,裂纹最长为160 mm,模具失效,与模拟分析的失效位置和使用寿命一致,证明该模拟分析方法的准确性,实际模具失效位置如图9所示。
图9 实际生产模具失效情况
3模具结构优化及疲劳数值模拟分析
3.1 模具结构优化
优化后的模具采用3工序方案,模具结构优化如图10所示。从图10可以看出,优化思路主要有2个:①取消模具斜楔反侧的桥架结构;②分解模具的翻边整形成形力。最终斜楔修边翻边整形模具改进为直修边翻边整形模具+斜楔翻边整形模具。第2工序是直修边翻边整形模具,取消斜楔结构;第3工序是斜楔翻边整形模具,没有产生废料,无需废料滑落通道,取消桥架结构。
图10 模具结构优化
(a)原模具结构 (b)优化后模具结构
3.2 优化后模具疲劳寿命数值模拟分析
优化后的下模座应力分布如图11所示,下模座反侧处等效应力为2.97 MPa,整副模具结构的应力状态改善明显;疲劳寿命模拟分析结果如图12所示,下模座疲劳寿命为100万冲次,满足顶棚模具设计需求。
图11 应力分布云图
图12 疲劳寿命模拟分析结果
▍原文标题:顶棚模具疲劳寿命分析及结构优化
▍原文作者:孙飞李鑫锋牛灵凯夏弦刘中汉马超
▍作者单位:东风本田汽车有限公司