应用有限元分析软件制作2种材料的力学性能材料卡片,编辑BG700L和BG960L高强钢材料的密度、杨氏模量、泊松比等材料参数,并将真实应力应变曲线导入有限元分析软件中,所制成的BG700L和BG960L高强度汽车大梁用钢的材料卡片数据如图2。
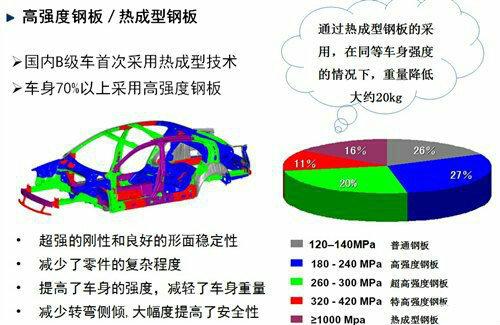
2. 汽车大梁有限元模拟分析2.1 有限元模型的前处理
建立某商用车型大梁的三维几何模型,为保证仿真模拟分析的准确程度,将模型的设计尺寸与真实零件的设计尺寸比例设置为1:1,几何模型如图3所示。使用Hypermesh前处理软件对模型进行几何清理与网格划分,网格标准尺寸取8 mm×8 mm,网格单元类型为壳单元,网格数量为103955个。大梁的上下板厚都为10 mm,加强板厚度为5 mm,整体质量为440 kg。在强度仿真模拟分析中材料分别选用BG700L和BG960L。在汽车大梁的强度分析过程中,设定汽车载重量为20 t,将20 t的载重量耦合到大梁上板,模拟汽车大梁的承重状态。为了能够满足车辆行驶过程中的最大承载能力的设计要求,在此条件下,对整个汽车大梁施加2.5g(g为重力加速度)的加速度载荷,来模拟行驶过程中的最恶劣的极限工况。通过约束A点来模拟前悬架的板簧支撑作用,约束B、C、D、E四点来模拟后悬架的板簧支撑作用,其中对A点约束123(XYZ向位移)方向自由度,而对B、C、D、E四点约束3(Z向位移)方向自由度[10−11],约束方式如图4所示(RBE3代表柔性连接)。
2.2 汽车大梁强度分析将Hypermesh软件中输出的设置文件导入有限元分析软件中进行求解,求解后的输出文件再导入Hyperview软件中进行后处理并输出仿真结果,本文应用Von Mises应力作为计算应力和判断标准。
不同的约束方式和载荷加载方法会对仿真结果产生影响,所以本研究在相同的约束和加载条件下,分别对BG700L和BG960L 2种材料制成的汽车大梁进行了分析对比。图5为分别为相同加载和约束条件下,采用BG700L和BG960L 2种材料制成汽车大梁的应力云图。从图5中可以看出,因为汽车大梁在受载时还处于弹性变形阶段,所以采用2种材料的模型的应力一致。在相同的加载和约束条件下,BG960L材料的制成的汽车大梁的应力与BG700L材料的最大应力都为699.8 MPa,应力均小于屈服强度,均在安全使用范围之内。
为了提高材料的利用率,达到减重和节约成本的目的,对此模型进行了减重处理,将大梁模型的上下板厚都减薄至8 mm,加强板厚度减薄至4.5 mm,减重后质量为355 kg,减重率约为20%。使用相同的分析方法,对减重后的汽车大梁进行强度分析,材料选择BG960L。图6为减重后汽车大梁的强度分析的应力云图。从图6中可以看出,减薄后的大梁最大应力位置处于模型的最下侧,与减重前基本一致。最大应力为874.3 MPa,比较减重前有所增加,应力还未达到材料屈服强度1070 MPa,能够满足汽车大梁的强度工况的使用要求,并且存在进一步的减薄潜力。
2.3 汽车大梁刚度分析
为了进一步验证减重的可行性,进行了大梁减重前后的刚度分析。刚度的分析方法如图7所示,分析方法与强度分析类似,对A点约束123方向自由度,而对B、C、D、E四点约束3方向自由度。因为零件的刚度只与材料的杨氏模量、泊松比以及零件的结构有关系,而BG700L和BG960L的杨氏模量和泊松比一致,所以本研究只对比了BG700L原设计方案和BG960L减重方案的刚度。图8为减重后的力与位移曲线,减重前加载点的Z向位移为0.77 mm,减重后加载点的Z向位移为0.9 mm。在线性计算过程中,刚度值为力和位移的比值,因此减重前大梁的刚度为266 kN/mm,减重后刚度为203 kN/mm。此车型商用车设计要求为加载点的Z向位移不能大于3 mm,而减重后的位移量并没有明显的增加,并且在安全使用范围内。
3. 结束语以高强度汽车大梁用钢BG700L和BG960L为例,针对强度工况和刚度工况进行仿真并进行结构优化。建立静态力学性能材料卡片,并应用到汽车大梁的强度和刚度仿真模拟分析中,研究结果表明:
(1)建立高强度汽车钢BG700L和BG960L的材料性能卡片,应用于强度有限元分析,提高强度模拟分析的准确度,对于汽车的轻量化和选材具有指导意义。
(2)BG960L材料的屈服强度和抗拉强度明显优于BG700L,分别对采用2种材料制成的某车型大梁进行强度分析,模拟结果显示采用BG960L高强度钢的大梁钢力学性能良好。减重后采用BG960L制成的汽车大梁的最大应力远小于屈服强度,具有良好的减重空间,并且能够达到认证要求。
(3)应用有限元分析软件,对减重前后的结构进行刚度分析,并对比了分析结果。模拟结果显示减重后的位移量比减重前的位移量增加0.13 mm,没有明显减弱,在合理使用范围之内。
文章来源——金属世界