1零件结构及工艺性分析
图1所示零件分别为背门外板下段及顶盖后段,材质分别为CR180和CR4,料厚均为0.85 mm,材料力学性能如表1所示。
图1 背门外板下段及顶盖后段
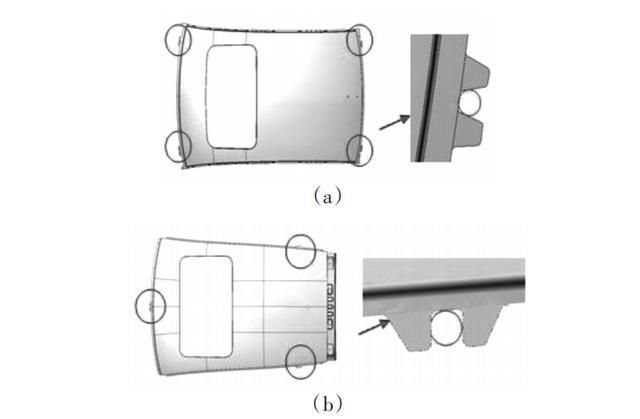
表1 CR180和CR4材料力学性能
从图1可以看出,2个零件深度较浅,且深度基本一致,可采用阻力较大的拉深筋控制拉深时的材料流入量。零件为轴对称形状,通过对拼工艺一方面可以提高生产效率;另一方面也可以使拉深工艺补充更加有利于零件的成形。
2有限元仿真模拟
利用三维造型软件对零件模型进行工艺补充,采用AutoForm软件建立有限元模型,如图2、图3所示。
图2 背门外板下段有限元模型
图3 顶盖后段有限元模型
经仿真优化得到符合工艺要求的结果,成形极限、材料流入量结果如图4~图7所示,仿真结果显示2个零件的成形性良好,材料流入量均接近于零,满足工艺要求。
图4 背门外板下段成形极限
图5 顶盖后段成形极限
图6 背门外板下段材料流入量
图7 顶盖后段材料流入量
3各工序工艺概述
考虑冲压效率及机床的承载能力,先将2个零件分别与绕自身旋转180°后的零件对拼,并保留适当的拼接距离,如图8中的a、b所示,选择双槽工艺。
图8 对拼后的零件
冲压工艺共有5道工序,分别为拉深、修边侧修边冲孔、修边侧修边整形、侧冲孔侧整形修边、修边翻边。
图9所示为拉深工序,通过调整拉深补充及拉深筋造型调整2个零件的成形力和压边力,最终保证2个零件成形力和压边力基本一致,以避免零件成形过程中因成形力不一致造成模具偏载,2个零件的冲压中心距机床中心的距离也需一致。模具中心1与机床中心重合,另外通过调整局部工艺补充面2,使零件局部非对称,在零件调试过程中起到防止零件反向放置的作用。3为凸模分模线,通过优化分模线的形状位置来优化零件的成形性。4为阻力较大的拉深筋,用于提高零件的塑性变形能力,并避免因材料流入量不稳定而造成最终成形零件质量不稳定的现象。
图9 拉深工序
图10所示为修边侧修边冲孔工序,将部分废料沿修边冲孔轮廓线5切除,为后工序分离、翻边整形做准备,并预冲后工序非对称检查孔。通过使用二次切断刀6,保证废料尺寸满足技术要求。适当缩小2个零件的中心距,以避免模具尺寸过大。
图10 修边侧修边冲孔工序
图11所示为修边侧修边整形工序,将大部分的废料沿修边轮廓线8切除,9为整形分模线。背门外板下段:对分模线以内的区域整形为零件形状;顶盖后段:对环形分模线以外区域进行整形,为后工序二次整形做准备。通过使用非对称检查孔7、10,避免零件成形过程中位置放反。
图11 修边侧修边整形工序
图12所示为侧冲孔侧整形修边工序,背门外板下段:将其余废料沿修冲轮廓线12切除,2个零件分离;顶盖后段:冲孔。将二次预成形区侧整形为零件形状,13为侧整形分模线。通过使用非对称检查孔11,避免零件成形过程中位置放反。
图12 侧冲孔侧整形修边工序
图13所示为修边翻边工序,背门外板下段:将需要翻边的区域沿翻边分模线14翻边成形,得到2个相同的背门外板下段零件。顶盖后段:将需要翻边的区域沿翻边分模线14翻边成形,其余废料沿修边轮廓线15切除,2个零件分离,得到2个相同的顶盖后段零件。通过使用非对称检查孔16,避免零件成形过程中位置放反,适当增加2个零件的中心距,保证模具空间满足设计要求。
图13 修边翻边工序
4最终零件及检测结果
现场调试成形得到最终零件,如图14、图15所示。现场零件成形过程良好,与仿真分析结果一致。图16、图17所示为最终零件的检测结果,2个零件的型面偏差符合技术要求,仅局部区域超差。
图14 背门外板下段零件
图15 顶盖后段零件
图16 背门外板下段检测结果
图17 顶盖后段检测结果
▍原文作者:解松 1孔悦晖 2王耀 3赵玲玲 1解衍强 4
▍作者单位:1. 天津轻工职业技术学院;2. 天津津荣天宇精密机械股份有限公司;3. 河北工业大学