零件尺寸偏差,设计公差累计,工装影响,工艺及操作人员影响四个方面
大家好,我是汽车设计工匠,今天我们主要说一下前两个方面:
第一方面:零件尺寸偏差
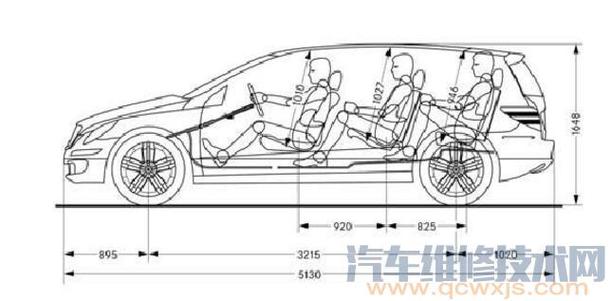
某车型前大灯与前保间隙大(标准5~4.5mm,实测6.0mm),查看整车数据,整车数据显示右前大灯立柱安装点(02-12R)Z向偏高0mm,供应商右前大梁大灯立柱安装点检具数据与整车表现一致,结果判定尺寸偏差来自零件尺寸偏差。
第二方面:设计公差累计
某车型前轴安装孔挡孔,员工在攻牙返修过程中导致孔大。挡孔方向为Y向,故障模式为车身大梁螺母孔孔距<前轴安装孔0.5~0mm。
尺寸链分析:
A、Y方向,前轴基准定位孔的安装位置度:15-18=0.7;
B、A1尺寸公差15(0~0.1),位置度公差0;
C、B1尺寸公差15(0~0.1),位置度公差0;
D、螺母孔2个均为M12,位置度公差+/-5;
按极值法计算,累积误差+/-5正态分布各环公差计算公式:
A、封闭尺寸A0=18×2-0.7=66mm;
B、前轴孔B1相对基准孔A1Y向尺寸为:18+66=15.46mm;
C、但实际上该孔为13×15的长孔;
同理:
A、前轴孔A2相对基准孔A1Y向尺寸为:18+8=15.6mm;
B、但实际上该孔为15的圆孔;
C、挡孔超差概率是6%。
将孔加大的可行性分析。
考虑到11的安全系数,支承面的最大应力[σ]不能超过212MPa。A2孔更改1和更改2的支承面的应力已经超过了[σ],安全系数降低。更改3的支承面的应力已接近屈服极限,不能接受。B1孔由Φ13×15改为Φ13×16,承面的应力虽然小于[σ],但也非常接近了。材料是ST37-2G,屈服强度是235MPa。摩擦系数是0.10~0.16,按照0.10计算。扭矩是68~88NM,按照88NM计算。计算K=0.133,螺栓夹紧力=55138N,具体数据如下表。
将A2孔由Φ15改为15×16的长孔,将B1孔由13×15改为13×16的长孔,进行CAE分析:模拟螺栓扭矩为88N·M,加入整车工况和发动机工况,具体数据见下表。
CAE分析的安装孔附近的应力靠近约束点,造成分析结果偏差大,但可用于对比分析,孔加大后的应力最大增加了6%~9%,安全系数也就降低了。
大家好,我是汽车设计工匠,关注我不迷路。
综上:将A2孔由Φ15改为150.1×15.80.2的长孔,将B1孔由13×15改为130.1×15.80.2的长孔安全系数降低了,理论分析结果还在可接受范围内,结果判定尺寸偏差来自设计公差累计。