一、翻边模的质量要求
翻边模的质量要求与修边模颇有相似之处。一般应使工作表面与制件贴合状态良好,翻边线要准确适当、折曲状态良好,不使制件变形、皱折或留下表面斑痕,模具机构动作协调可靠,操作方便。
制造镶块翻边凸模的技术要求:
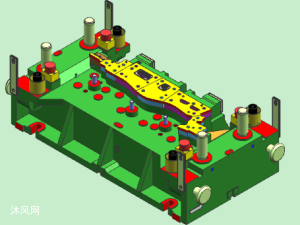
镶块收缩后,工作部分的形状和尺寸与主模型一致;镶块张开后与冲制件外壁不碰,又能顺利地取出冲制件。
制造镶块翻边凹模的技术要求:
镶块张开后,凹模轮廓的形状和尺寸符合冲制件的翻边要求;而镶块收缩后要不影响前工序件进入工作位置。
滑键及键槽保证滑动配合,以达到张开与收缩动作灵活的目的。
二、翻边模的制造工艺要点
制造凸模的工艺要点:
加工型面时,为保证冲制件的质量,凸模在仿形铣加工前,将各镶块按收缩位置固定在工艺固定板上,划出冲模中心线。仿形加工时,通常按拉深件进行仿形加工,选择铣刀直径时,应考虑制件的料厚。仿形加工后,尤其是在热处理后,把凸模镶块装在滑块上,必须用样架研修型面,保证其吻合,最后进行抛光。
凸模的翻边轮廓应按样板进行划线、铣和修磨加工,样板则按凹模轮廓加料厚。在样板上,除划有冲模中心线外,还应划出凸模镶块的内轮廓线和接合面线,以便于划线和精修时确定样板的位置。
制造凹模的工艺要点:
外轮廓加工时,应考虑凹模镶块张开后,其外轮廓的形状和尺寸符合冲件翻边要求,所以通常采用一块整样板来控制。粗加工按样板划线铣(插),热处理并打磨加工后,镶块固定在张开位置,按样板划线精修外轮廓。
为了保证各镶块张开与收缩动作灵活,在磨镶块接合面及斜楔滑动面时,应找正镶块上的键槽方向,并以键槽为基准,精磨镶块各面。
凹模镶块的高度应比凸模翻边处高度差一个冲制件的料厚。粗加工时,可按图样尺寸留磨量;精加工时,应按凸模翻边处的实际高度配磨(减去料厚)。
压料板制造工艺要点: 与修边模相类似,压料板的翻边线附近要仔细打磨抛光,特别是外缘翻边的场合,往往需要边打磨边调整,以防止翻边模工作时,造成覆盖件凸缘附近出现局部翘曲。
汽车覆盖件冲压成形应用实例4 “前门内板”的冲压工艺及模具
一、“前门内板”的工艺分析
“前门内板”属于汽车内覆盖件,它与“前门外板”通过点焊装配成前门,同时要求与前门框有良好的配合。其上有许多局部凸包、通孔、窗孔和边孔,不难想象,其基本工序中必含有拉深、切边和冲孔(含斜楔冲孔)。图所示为其制件简图。
“前门内板”属于不对称的覆盖件,其拉深深度浅而均匀,但是形状比较复杂,具有与“前门外板”相配合的凸缘面,尺寸较大,在其上分布
着许许多多大大小小的孔,这些孔的尺寸精度及孔之间的位置精度要得到保证,必须 尽量增加 刚性,为此要 利用反拉 深制出凸包,使孔分布在凸包上。拉深工序的精度直接影响到后续工序的精度,因此该零件的重点在拉深工序上。
“前门内板”风窗局部加工要领
该 零件还 有一个很 大的风 窗 孔在其边 框 部 位, 需要进行垂直和水平冲孔,另 外窗 孔 的周 边修 边线 并不 是直线,其上有些部位要通过整形制出小法兰,而且 下 边 缘 的 修 边 线 有 局 部 小 圆 角 。因此如何处理好风窗的冲压工艺就成为“前门内板”的难点之一,其冲压工序的安排,也大致决定了整个零件的工序安排。下面,我们以“风窗部位”为重点,兼顾考虑到模具的刚性及风窗某些特殊形状,要一次冲出风窗是不合理的,因为这样无法保证特殊形状部位的精度。同时,为了使各个工序中的零件各部位所受加工力分布均匀,则必须把风窗分成几个部分冲压,即先在需要整形和需要水平斜楔冲孔的特殊部位冲出孔以留出后续工序整形及冲孔的空间;第二步再对特殊部位进行整形;第三步完成水平斜楔冲孔和余下部位的修边。若把二、三两工步合为一步完成,可能使整形模和水平冲孔模之间发生干涉,因此,拉深后至少还需三步才能把零件加工出来。图所示为风窗局部的加工要领 ,这一步也是由其他部位的 加工工艺决定 。图所示为周边局部的加工要领,拉深后必须进行“全周修边”,然后进行“全周整形”,接着才能在成形后的零件外周上冲孔。
总 的来 说 ,加工工艺和工序的设计必须根据制件图上从冲压加工看具有代表性的断面和各个拐角部分的成形要求,并在确保制件精度的情况下依次设计必要的工序。应该对零件从机能来说是重要的和不重要的部分区别对待。一般应注意下列事项:
一般用作外表的钢板件。喷涂装饰以后表面质量有特殊要求的,同一曲面应一次成形。如果分两次成形,其交接处会残存不连续的面,表面质量明显恶化,因此需要选择合适的冲压方向。
焊接面存在皱折一般就焊接不好,有回弹则表面位置不准、装配困难或者出现装配后精度不良的情况,所以不规则的形状只能用拉深工序把焊接面制作出来。当焊接面用弯曲工序做出来时,应该选择没有变薄的冲压方向作为加工基准用的孔,如在冲压工序早期就冲出来,当工序进行下去时孔会变形和偏移,所以在成形之后冲孔。图所示为冲孔的一些规则在本零件加工中的应用。图表明关联孔必须在同一工 序中加 工 ,表明大孔和小孔接近时,先冲大孔,后冲小孔。
( 一 )落 料 工 序
根据以上的基本原则及该零件的工艺特点,需采用落料、拉深、切边冲孔及冲孔等工序制作。现分述如下:
见 图“前门 内板”采 用薄板制造。由于该零 件不是规则的形状,如用整块
规则矩形料进行拉深,显然会造成材料的巨大浪费,给后续工序废料清除带来麻烦,更主要的是在拉深工序中压料面分布不均,不能保证零件各部分压边力的均匀分布。为此,要有一道专门的落料工序使坯料接近拉深后的坯件形状,
(二)双动拉深工序
本拉深工序的加工内容是进行全体成形,从而得到一个接近于零件的形状。而覆盖件的拉深件的确定具有相似性,为此讨论“前门内板”拉深工序之前,我们首先必须回顾一般拉深件的确定方法,并根据一般拉深件的拉深特 点来研究“前门内板”的拉深工艺特点。
“前门内板”属于不对称的覆盖件,确定与汽车位置垂直的拉深方向,制件上没有负角部分,能够保证凸模进入凹模。由于“前门内板”形状复杂,凸包多而分散,开始拉深时毛坯与凸模的接触处较多,故受力均衡,毛坯不会在凸模顶部窜动;又因凸包形状低于压料面形状,故不会使拉深件的内部形状成大皱纹和材料重迭,“前门内板”属于深度变化不大的零件,也就 保证了压料面各部门进料阻力均匀 ,在拉深过程中可 防止拉深毛坯窜动,即保证了表面质量。“前
门内板”的各道工序中无翻边工序,只 需在覆盖件上加必 要的工艺补充部 分即可构成拉深件 ,并且均采用垂 直修边。同时在修 边及修边后的定 位中主要采用工序件外形、侧壁形状定位。后 道工 序件在冲模上 的位置除了拉 深翻转转入后续工 序外,其余工序是一致的。
由于拉深件形状复杂,本工序采用双动压力机。采用双动压力机的优点是:单动压力机的压紧力不够,一般有气垫的单动压力机,其压紧力等于压力机滑块压力,单动压力机的压紧力只能整个调节,而双动压力机的外滑块压力可以四角单独调节,从而起到调节拉深模压料面上各部位的压边力,控制压料面上材料流动的作用。
单动压力机的拉深深度受到一定的限制。单动拉深模的压边圈是刚性的,如果压料面是立体曲面,形状的不对称会致使压料板偏斜,严重时失掉压料作用。该零件拉深的压料面大部分本身就是覆盖件的凸缘面,此时的修边线一般就在拉深件的压料面上,通过以后的垂直修边切除多余部分。通过对该零件断面尺寸的分析,大多数断面的部分材料的延伸率基本满足工艺要求。
图可以看出本零件压料主要有水平压料面
和向下倾斜的压料面。本拉深件主要采用安置拉深筋的方式来调节进料阻力,筋布置在拉深件四周的直线部分,增加了进料阻力,使圆角部分与直线部分进料阻力均匀。
( 三 )切 边、冲 孔 第一工 序
如 图所 示,上道拉深工序的制件翻转,进入切边、冲孔工序。本工序加工内容有:修边、全周修边、冲孔。修边废料切成如图所示的几段 。
分析本工序加工内容,我们可以看出,此工序完成了零件所需的大另一方面把三个通孔按图示布置,以方便两工序间的衔接。对于一些安装门锁、摇把等连杆机构有较严格相互位置关系的关联孔,都安排在同一道工序中冲制,以满
足尺寸要求。
全周修边是为了切去工艺补充部分,它
是拉深件后续工序中一个必不可少的环节。
(四)切边、冲孔 第二工序
制件经上道工序后位置不变地转入此道工序进行切边冲孔。本工序的主要加工内容有:冲孔、整形、全周整形及图示窗口部分整形。
从加工内容可以看出,本工序所冲的孔大多为小孔,在废料处理时应考虑这些小废料的收集,并尽可能少用废料箱。不能直接落入废料箱的废料可
采用溜槽滑入废料箱。
此工序中有许多相关联的孔:椭圆孔两个, 长方孔两个。长形孔 要避免和斜楔冲孔发生干涉。
通过整形将前面几道工序中不符合零件形状的部位修正过来,把未加工出的形状压形出来,使制件的外形符合零件的最终尺寸和形状。
此处的凸缘弯曲是为下道工序的冲孔作准备的,这种先弯曲后冲孔的工序安排符合成形后冲孔的原则。
(五)冲孔工序
二、“前门内板”各工序的冲压模具
下面介绍完成这些工序所需模具的基本结构和动作原理。由于拉深工序在整个零件的加工中具有重要地位,且其模具结构(双动拉深模)在大型覆盖件模具中有普遍的代表意
义,因此在模具结构分析时,我们将重点讨论拉深模。
注意到成形左右前门内板所需模具是不同的,故除落料模只需一副模具外,其余工序所需模具均为左、右各一副。本套模具有:落料模、双动拉深模、切边冲孔模和冲孔模。
( 二 )前 门 内 板 落 料 模
本落料模在单动压力机上使用,采用倒装式结构,主要由下模托板 、上压料板 、下模和上模 等部分组成。其中上模与上压料板之间利用导板导向,并且采用侧销和安全吊杆相结合的双重安全机构,在上模上行时起到吊起上压料板的作用。其中吊杆在模具正常工作时不起作用,仅当安全侧销出意外时(如被切断),它才托起上模,起保险作用。为了防止和阻止模具启闭时人手或其他异物进入模具中而发生意外,下模上还设有安全护板。上压料板和上模之间安装强力弹簧以使上压料板具有压料作用。上模和下模之间通过导
柱导套导向。下模托料板上装有滚珠滑轮以方便送入平面板料。坯料的取出及送入均通过橡皮滚轮滑道,并由人工进行。
( 一)“ 前 门 内 板”落 料 模
该模具动作原理如下:滑块下行时,带动上模及上压料板向下运动,
上压料板将平面板坯料向下压,直至上模压板将坯料压 紧在 下 模上 ,然
后上 压料 板停 止运动, 滑块 继 续向 下运 动时 ,上 模切 下废料。滑块回
程时,上模上行,上压料板也随之向上运动,使加工后的坯料脱离接触失去压紧力后,下模托板将之托起,滑块停止运动,工作人员即可取料。
1-安全侧销2-安全吊杆 3-下模托板
4-上压料板5-下模6-上模
( 二 )前 门 内 板 拉 深 模
该拉深模见图,在双动压力机上使用,故称为双动拉深模,主要由凹模、压 边 圈 、凸模 、顶出器 等几部分组成。其中,压边圈与压力机的外滑块相连。其基本的动作过程为:压力机外滑块下行时,压边圈随之到达下死点,将毛坯压紧在凹模压料面上并保持不动,内滑块后于外滑块向下运动,凸模也随之下行,将毛坯进行拉深直到下死点。拉深完成后,凸模随内滑块先回程,压边圈在保持一段时间静止不动后即随外滑块向上运动,然后顶出器将成形后的拉深件顶起再人工取出。
( 三 )前 门 内 板 切 边、冲 孔 模
该模具在单动压力机上使用。该模具主要由上模、下模、压板、废料刀、上模镶块、下模镶块、升降台等组成,其中上模与上模压板之间安装有强力弹簧,使上模压板具有压料作用,它们之间采用导板导向,并且有侧销和安全吊杆相结合的双重安全机构,可在回程时吊起上模压板,使之与上模一起上行。模具的基本动作原理:滑块下行过程中,上模与上模压板(推件块)也随之向下运动,首先压料板接触制件停止运动,而上模继续向下运动,它们之间的压料弹簧压缩,使压板的压边力愈来愈大,从而达到理想的压边力,此时上模和下模相互作用在制件上进行切边、冲孔。上模随滑块回程,压料板可对制件起顶料作用,直到在侧销带动下,也随上模上行脱离制件。制件在升降台的作用下被顶起,可人工取料,转入下一道工序。这种冲模结构属于垂直修边模。其模具的主要特点是修边冲孔。
1-升降台
2-压板 3-下模 4-上模
( 四 )前 门 内 板 切 边、冲 孔 模
该模具在单动压力机上使用。和上套模具相似,上模与压板之间安装有强力弹簧,采用双重安全机构,之间采用导板导向。上模与下模之间采用导板和两个导柱导套双重导向,这样就可使整形、弯曲、冲孔的精度得到保证。
基本动作原理与上工序的模具相似。上模下行,带动压板首先接触制件起压料作用,压板停止运动,上模继续下行,压边力达到合理值时,上模首先完成冲孔,接着进行整形、弯曲。完成工作后上模首先回程,压板不动起卸料作用,后在板边作用下随之回程,气动顶料装置可顶料,以便于手工取料。
1-下模2-斜楔冲孔机构3-上模压板4-上模
( 五 ) 前 门 内 板 冲 孔 模
该模具在G型单动压力机上使用。该模具主要由上模、下模、上模压板和不同位置的斜楔冲孔机构组成。
本模具的最大特点是使用了斜楔冲孔机构。汽车覆盖件常有一些和冲压方向不一致的孔,这些孔可分为两类:一类与冲压方向垂直;另一类与冲压方向成一定夹角(即斜面上的孔)。对于水平方向的孔一般采用单向斜楔机构,而对于斜面上的孔,则采用双向斜楔机构。由于该模具有斜楔冲孔机构,故承受较大的侧向力,同时为了使导向精确,采用导柱导板联合导向,并将导板设置在与导柱导套同一轴线上,有效地保护了导柱导套的配合精度。
1-下模2-斜楔冲孔机构3-上模压板4-上模