一,问题描述
Auto form是专门针对汽车工业和金属成形工业中的板料成形的仿真模拟软件,用于进行复杂的冲压成形分析和优化冲压工艺方案。为了验证Auto form软件对顶盖尾部顶面产生波浪问题进行分析的准确性,在现有的条件下进行了2组试验,从试验结果看,软件分析结果与实际生产相符程度在90%以上,如图1所示。
图1 CAE分析结果与实际结果对比
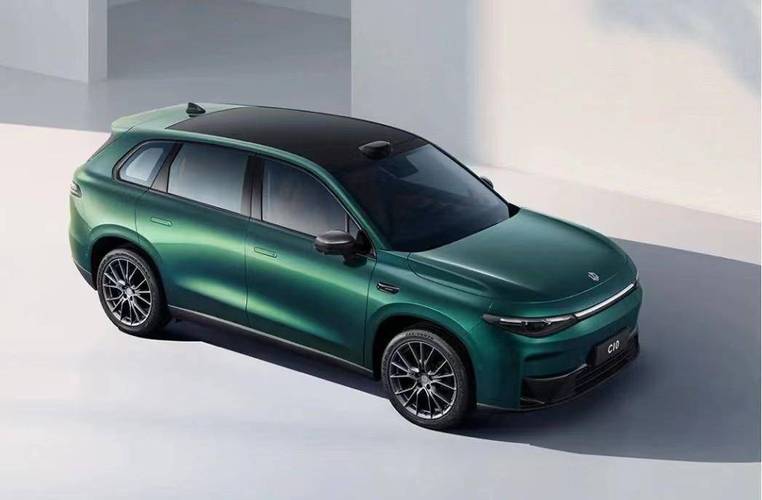
图2 拉深件
图3 侧整形后零件
图4 修改侧整形后零件
某两厢汽车顶盖(简称A顶盖)的冲模开发过程中,拉深件顶面并无波浪产生,如图2所示,但在第2工序侧整形后,尾部顶面产生了严重的波浪问题,如图3所示。最初推断是第2工序的压料板研合率不足,导致顶面压力不够,侧整形带动尾部顶面的板料发生轻微位移,造成波浪的产生。但研合率达到要求后,波浪问题并没有减轻。后经CAE分析,发现制件在第2工序整形回弹后发生的波浪现象,并不是在整形过程中产生的波浪。通过CAE模拟分析,在修改侧整形部位后,波浪消失,如图4所示,说明波浪属于弹性变形范畴,并没有发生塑性变形。
二,原因分析
通过对比拉深工序和整形工序内部应力CAE分析结果,拉深工序件主应力大部分大于0,局部次应力小于0,但绝对值较小,接近于0。整形工序件出现大部分主应力小于0的情况,次应力全部小于0,且绝对值较大,如图5所示。这说明整形回弹后给顶盖尾部顶面带来了较大的压应力,较大的压应力是尾部顶面产生波浪的主要因素。两厢汽车的尾门安装方式决定了两厢汽车顶盖尾部的结构必然会有负角,从而决定了两厢汽车顶盖必须采用尾部侧整形的工艺,最终导致顶面存在较大的压应力,给顶盖尾部顶面产生波浪提供了驱动力,这也是顶面产生波浪问题的必要条
图5 内部应力分析
图6 3个顶盖的分析结果对比
既然产生波浪的驱动力必然存在,理论上类似结构的顶盖应该都存在类似问题,但通过与多个车型比较,发现并不是所有具有类似结构的顶盖都存在尾部顶面波浪问题,或波浪问题与此车型同样严重。对3种类似车型的顶盖进行比较,如图6所示,顶盖的结构大同小异,材料的材质和厚度略有不同,CAE模拟分析结果显示,尾部顶面同样有较大的压应力存在,即都有尾部顶面产生波浪的风险,但是结果却是车型A有波浪,车型B和C没有波浪(分析结果与实际一致)。
图7 A顶盖不同方案的分析结果
基于以上疑问,对A顶盖进行了不同材质、不同厚度、不同形状的CAE模拟分析,如图7所示,从对比中寻找原因。纵向对比发现,同是DC03的材质,0.8mm厚度的顶盖波浪问题比0.7mm厚度的顶盖波浪问题要轻。横向对比,相同厚度不同材质的顶盖波浪区别并不明显。改变侧整形第一触料点的分析结果显示,波浪位置虽然和原始状态稍有区别,但并没有改变产生波浪问题的本质。延长顶面加强筋,其分析结果要优于其他结果,但并未完全解决产生波浪的问题。从分析结果来看,无法找出合理解释3种顶盖产生不同波浪问题的原因。
在解决波浪问题的过程中,用CR210B2材料进行了试验,试验效果理想,但发现试验结果和CAE分析结果差别较大(CAE分析结果很差,同样存在波浪)。前文提到,经过验证CAE分析结果与实际生产相符度在90%以上。后来发现CR210B2材料为电镀锌钢板,实际上电镀锌钢板的抗凹性要强于非镀锌板,而Autoform软件进行冲压模拟分析时不能区分镀锌板与非镀锌板,这也是CAE分析结果与实际生产的结果产生差异的原因。因此推断抗凹性的差异是3个顶盖具有不同结果的根本原因
三,抗凹理论概念
抗凹理论是指汽车覆盖件在受到力的作用下,抵抗变形的能力。抗凹理论有2个概念:一是局部凹痕抗力,指抵抗塑性变形的能力;二是抗凹刚度,指抵抗弹性变形的能力。因为前面已经分析,波浪属于弹性变形范畴,针对此问题,只借鉴抗凹刚度理论进行分析。引用陈莲峰等抗凹理论试验结果,说明抗凹刚度与材质、厚度和形状的关系。试验采用3种不同材质的板料对某车型翼子板拉深件的3个不同位置进行抗凹试验,如图8和表1所示。
图8 翼子板试验取点位置
经过抗凹理论试验得出3组数据,如图9~图11所示,抗凹刚度曲线的斜率越大,抗凹刚度越强。
从图9可以看出:随着材料屈服强度的提高,零件的抗凹刚度略有增强,但差别不大。
图9 3种材质在相同位置(Ⅱ点)的抗凹刚度
图10 180BH不同压边力下产生的抗凹刚度(Ⅲ点)
从图10可以看出:在一定范围内,拉深时,随着压边力的增大,零件的抗凹刚度略有增加,变化不大,当压边力增大到一定程度时,板料厚度减薄过大,厚度变小,零件的抗凹刚度出现大幅度降低,说明材料的不同厚度对零件的抗凹刚度影响比较大。
图11 180BH不同位置的抗凹刚度
从图11可以看出:零件型面的不同曲率半径对零件的抗凹刚度影响比较明显,曲率半径越小,零件的抗凹刚度越强。
四,抗凹理论分析及验证
经过分析发现,改变材质和材料厚度,对解决此车型顶盖的波浪问题并没有明显的效果,即改变材质和厚度,其抗凹刚度并没有明显的变化。材质和厚度并不是3个顶盖产生不同波浪问题的主要原因,C顶盖的厚度为0.65mm,小于A顶盖的0.7mm,理论上C顶盖的抗凹刚度要弱于A顶盖的抗凹刚度,C顶盖的波浪应该比A顶盖严重,但事实正好相反(见图6)。经过进一步分析发现:B顶盖和C顶盖的尾部顶面的曲率半径皆在4000mm左右,而A顶盖的曲率半径接近于6800mm,如图12所示
图12 3个顶盖尾部顶面曲率半径对比
顶盖曲率半径的差异是A顶盖的抗凹刚度明显弱于B顶盖和C顶盖的主要原因,直接结果是导致A顶盖尾部顶面的抗弹性变形的能力差,在压应力的作用下,产生了严重的波浪。为了验证此结论,对A顶盖的尾部顶面进行了调整,曲率半径由6800mm调整为4000mm,其余型面不变,进行CAE模拟分析,分析结果符合预期,如图13所示。
图13 A顶盖尾部顶面曲率调整后的分析结果
抗凹试验,方案1为初始状态;方案2为顶面加强筋延长到尾端状态;方案3为尾部顶面曲率半径调整到4000mm的状态。鉴于顶盖的曲率半径较大,采用直径为ϕ25.6mm的压块(见图14),以每次0.5mm的位移增量对A顶盖尾部顶面P点进行反复加载、卸载,重复7次
图14 抗凹试验示意图
模拟试验计算完成后,从Auto form软件pro⁃cessdata界面提取模拟试验数据,得到如图15所示的试验结果。
图15 抗凹刚度模拟试验方案及结果
从模拟试验结果看,在抵抗小于约0.8mm的微观变形时,3种方案的顶盖抗凹刚度强弱依次为:方案3大于方案2远大于方案1;在抵抗大于约0.8mm的宏观变形时,3种方案的抗凹刚度强弱依次为:方案2大于方案3大于方案1。方案2顶面加强筋延长到尾端,在局部范围内,原有面的抗凹刚度本身并没有加强,在较大的范围内,通过加强筋的延长使整体抗凹刚度得到了提升,因此在约0.8mm的位置出现了方案2和方案3的抗凹刚度曲线交叉的情况。
A顶盖产生波浪是在模具调试阶段,如果此时按照方案3整改,会牵扯到与之匹配的尾门的形状更改,改动量较大,改动成本高,考虑到以上因素,采用了改动量较小的方案2,虽然方案2还存在轻微的微观变形,但可以接受。
两厢汽车顶盖尾部侧整形后回弹,导致尾部顶盖内部存在压应力,如果压应力超出顶盖此处的抗凹刚度的承受能力,就会产生波浪,此为顶盖产生波浪的驱动力,且此驱动力是客观存在的,无法消除。可以通过以下措施增强零件的抗凹刚度,减轻顶盖尾部顶面波浪缺陷的产生。
1
保证顶盖尾部顶面截面曲率半径R≤4000mm,全面提高抗凹刚度。
2
如果顶面有加强筋,加强筋延长到尾端,通过提升局部抗凹刚度加强整体的抗凹刚度。
3
增加材料厚度可全面提高抗凹刚度。
4
采用电镀锌板,提高抗凹刚度。
5
材料等级提高(采用屈服强度大的材料),对提高抗凹刚度有一定帮助,但作用有限。