后背门内板作为冲压件中最复杂的制件之一,正 是由于这个造型特征,决定了模具零件型面的复杂性 和拉伸深度的差异性,导致拉伸成形时板料走料不 均匀,应力应变不均匀,易出现起皱或开裂等质量问 题。后背门内板做为与后背门外板及后背门护板匹 配件,具有很高的尺寸精度,包括轮廓尺寸、孔位尺寸 及局部形状特征尺寸等。
现以某车型后背门内板为例,阐述制件起皱与开
裂产生的原因,同时结合有限元仿真模型对制件进行 分析,通过调整压边力,优化拉伸筋位置、参数,增加 工艺切口的方法等,解决制件在拉伸过程中产生的起 皱、开裂等冲压件质量问题,以满足制件尺寸与義面 质量要求,并为其相似制件模具工艺排布及设计提供 参考。
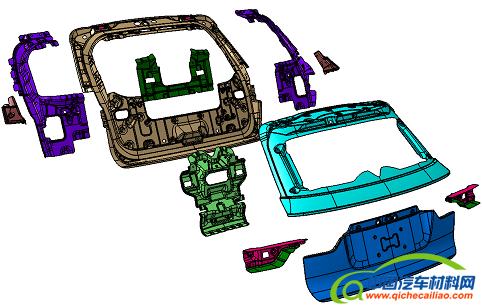
图1所示为某车型后背门内板结构,由特征复 杂的空间自由曲面构成,无法釆用解析形式表述, 只能采用参数曲面表达,成形工艺采用一次拉伸成 形,压合面后序整形完成。目前大多数制件拉伸模 由凸模、凹模和压边圈3个部分组成,由于零件型面 的复杂性导致制件在拉伸过程中局部变化的剧 烈。同时拉伸深度过深(凸模最髙点与最低点的高 度差达250mm)导致成形过程中板料流入不均匀, 成形不稳定,易产生局部起皱、开裂等缺陷,如图2 所示。
3后背门内板冲压工艺排布
图3所示为后背门内板冲压工艺排布,根据制件 造型特征考虑到冲压方向,拉伸深度及零件功能等要 求,确定冲压工艺为5道工序,分别是:①OP10拉伸; ②OP20修边+侧修边+冲孔;③OP30整形+翻边;④ OP40侧冲孔+冲孔+修边;⑤OP50侧冲孔+冲孔+修边。并确定每道工序的工作内容,如图3所示。
以上工序中拉伸工序是制件能否顺利生产的关 键,考虑到制件造型的复杂,也为了减小拉伸深度对 制件开裂、起皱的影响,拉伸模釆用反拉伸、上、下压 料结构,同时拉伸深度降低后也提升了制件的材料利 用率。具体结构如图4所示。
反拉伸具冇以下优点:①反拉伸材料流动方向与正拉伸相反,有利于相互抵消拉伸过程中形成的残余应力;②反拉伸时,材料弯曲与反弯曲次数较少,冷作硬化也少,有利于成形。正拉伸中,位于压料圈圆角部的材料,流向凹模圆角时,内圆弧成了外圆弧。而反拉伸中,位于内圆弧处的材料在流动中始终处于内圆弧地位;③反拉伸将原有的外表面内翻,原有外表面拉伸时的划痕将不影响外观;④反拉伸坯料与凹模接触而较正拉伸大,材料流动阻力也大,因而一般可不用压料圈。但坯料外缘流经凹模人口圆角时,阻力已明显减少,故大直径薄料拉伸仍需压料,以免起皱;⑤反拉伸的拉伸力可比正拉伸力大20%左右。
4开裂与起皱产生原因及解决方案制件开裂的主要原因是板料无法正常流人到开裂区域,导致制件该区域变薄率超过材料本身极限值,产生开裂现象。拉伸件在拉伸过程中开裂的原因很多,主要原因有以下几个方面:
①模具凸、凹模间隙配合不合理;
②压边力调整过大;
③材料的性能偏差;
④模具光洁度不够;
⑤模具拉伸筋设置不合理;
⑥模具凸模角过小等等。
针对该后背门内板窗框处开裂问题,通过以上方案调整后效果不佳。为此对这种复杂制件容易开裂的位S,通常在废料区设置工艺切口(常称为刺破刀)使材料流动充分,并在后续修边模中切除。由制件开裂裂纹趋势可知,成形过程中原工艺切口区域板料补充不足是造成开裂的主要原因。为验证工艺切口的大小及形状对制件开裂的影响,采用有限元模拟软件Autoform对制件进行成形性分析。
由于板料在模具拉伸过程中不断变化,板料刺破的时间对该处板料流动产生很大的影响,为此需对对 刺破刀高度进行持续调整。增加刺破刀高度10mm后 的CAE分析结果,采用提前刺破,危险截面的减薄率 由30%降低至25%,显著提升制件拉伸成形质量。在 此基础上对凹模进行优化,将刺破刀高度增加至 15mm并进行生产验证,减薄率由30%降低至18.5%, 如图5所示。采用该优化工艺后,制件成形质量显著 提升,起皱与开裂缺陷消除,制件轮廓与尺寸符合数 模要求,因此增高窗框内废料刺破刀以补充进料的方 案可行。通过上述分析结果来看,制件增加刺破刀后 制件开裂问题得到解决,刺破刀高度15mm,具体刺破 过程如如图6所7K。
冲压件起皱主要原因为拉伸过程中板料与模具型面的摩擦力不够导致板料流人过多,局部型面大于实际料厚。拉伸件在拉伸过程中起皱的原因很多,主要原因有以下几个方面:
①冲压件拉伸深度太深,制件成形的过程中板料流动过快;
②冲压件在拉伸过程中凹模/R角过大,造成板料流动过快;
③冲压件压料筋不合理,压料筋过小和位置不正确;
④顶杆的压力过小;
⑤模具定位设计不合理;
⑥凸、凹模间隙过大。
以上为冲压件拉伸过程中起皱的常见原因,在具体问题中需要具体的分析,根据冲压件的具体情况来查找具体的原因。针对该处起皱整改方案主要为2点;
第1点通过调整拉伸筋位置及尺寸,增加摩擦力,减少板料从外部流入;
第2点增大压边圈压力增加摩擦力,减少板料从外部流人,如图7所示。
拉伸筋是控制制件成形质量的重要手段,通过增大进料阻力、调整进料阻力的分布及材料流动的均匀性抑制起皱与开裂等缺陷。改变拉伸筋参数可以改变进料阻力大小,以满足不同形状制件的变形要求。针对拉伸筋进料阻力不足,对压边圈外侧增加2处拉伸筋具体位置如图7所示。将上模凸筋的高度由8mm增加至10mm、拉伸槽圆角由/?5mm减小至同时将拉伸凸模各特征圆角相应增大,并提升压边研合率,释放压边圈硬点,确保管理面在7〜10mm均匀着色。
优化拉伸筋参数后进行小批量生产验证,结果表明,优化拉伸筋尺寸后有效控制了材料的流动速度,制件顶部的起皱得到明显改善。同时对于压边力不足导致起皱产生的问题,原压力为1601调整为2001时成形满足质量要求。从上述CAE分析结果来 看,制件在实施增加压边力和调整拉伸筋等方案后起 皱问题得到解决。
5模具开发过程控制控制点1:模具型面研合,模具各工序型面研合如 表1所示。
模具型面研合是模具开发中最避本的工作,也是 最重要的一步,模具研合做的好坏直接影响制件的质 量及生产的稳定性,其中各工序中拉仲模是种中之 中;当研合不好时型面存在局部硬点,对应的压边圈 压料面与管理面亦存在不同亮度的压痕。此外,压力 机平行度与模具压边间隙的轻微变化,加剧了板料与 模具零件表面的接触应力与硬点分布的不均匀性。 由于硬点对压边间隙的变化非常敏感,且硬点的拉伸 阻力仅作用于局部区域,造成局部成形阻力过大,局 部板料减薄超过应变极限。
控制点2:拉伸模成形稳定性。拉伸工序模具极 限测试检查表如表2所7K。
冲压模具生产的稳定性评价体系越来越受到汽车 行业和模具行业关注。目前,在国内的模具行业内,冲 模制造过程中会经常出现冲模生产不稳定的现象, 即在模具工艺设计阶段,经过CAE软件分析制件成形 已经满足实际生产需求,但在实际调试阶段却出现制 件起皱、开裂等问题,或者模具调试合格后,在制件批 量生产时质量却出现较大波动等现象,这些现象导致 冲模生产稳定性差。因此在模具开发过程中需要对 制件生产稳定性进行控制,对料厚的减薄率和变形量 进行测定以及制件质量稳定性进行评价。
6结束语随着汽车工业的发展和汽车生产周期更新换代 频次越来越高,冲压SE对制件开发质量和周期有着 重要的作用,在冲压件造型、材料不断变化中,各种质 量问题也存在不同。本文主要通过对后背门内板拉伸中存在的质量问题通过CAE分析及模具开发过程 控制等手段最终幵发出满足要求的制件,对冲压模具 开发和制造有一定的参考意义。当然要设计、制造出 尺寸精度更高,面品质量更好的冲压件,需要在使用 过程中不断总结和完善。