2 问题产生原因分析及改进方案
2.1 制件造型分析
影响机理:图2所示A1区域和A2区域造型翻 边角度存在角度差,翻边面角度不一致导致棱线圆 角弦长 L 1 >L 2 ,制件成形后目视 A1 区域圆角比 A2 区域大,手触存在不光顺感。
改进方案:门侧处a-b段增加立面如图3所示, 车身 Y方向增加 3°拔模角,立面 h=3.5 mm,确保倒 角后还保持0.5 mm的小立面。通过增加0.5 mm有 效宽度的小立面,使A1与A2区域紧邻圆角部位的 翻边面角度一致,实现造型目视效果一致,手触 光顺。
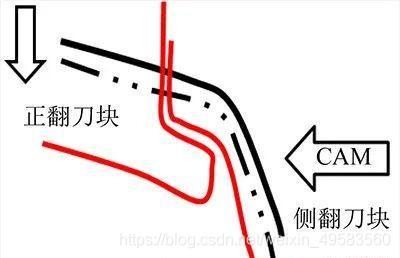
2.2 制件结构分析
影响机理:制件翻边面结构存在台阶,翻边刀 块接触时,台阶处存在间隙造成圆弧处积料,导致 圆角大小不一致,如图4所示。
改进方案:优化制件结构,取消台阶结构设计, 当台阶结构无法取消时,应尽量减小台阶高度,如 图5所示。
2.3 工艺方案分析
影响机理:翼子板一般采用4道工序成形,在工 序③设置正翻边与侧翻边同序交刀,若交刀角度不 良,会导致交刀范围内出现不同角度的二次翻边, 使圆角受到破坏,导致棱线不顺,如图6所示。
改进方案:一般翼子板门轴侧造型分缝切线与 车身 Z 方向存在夹角的关键角度为 10°,如图 7 所 示,根据夹角的大小有2种不同的处理方案。 夹角小于 10°时,通过旋转侧翻边的斜楔摆放 方向,实现侧翻边变为垂直翻边,同时正翻边也为 垂直翻边,当交刀的2个方向都是垂直翻边时,可避 免圆角被破坏,如图8所示。
夹角大于10°时,交刀设计先正翻边,且正翻边 方向为垂直翻边,并通过旋转侧翻边的斜楔摆放方 向,使侧翻边刀块只是起到包角作用,避免圆角被 二次破坏,如图9所示。
2.4 模具结构分析
影响机理:模具翻边工序的压力源布置、压料 面积以及侧翻边斜楔的分缝位置对棱线的光顺效 果有强相关的影响。压力源和压料面积设计不合理会导致翻边过程中的拉力将制件外露表面拉动, 出现棱线不顺现象。侧翻边斜楔分缝不合理会导 致出现压痕,也会造成棱线不顺现象。
改进方案:合理选择压力源大小和布置区域,P B =Lt&。其中,P B 为翻边成形力,L为翻边线总长度,t 为料厚,&为制件抗拉强度。压料力一般为翻边成 形力的 15%,成形外板类模具增加一倍压料力,压 料力 P=P B ×15%×2。布置原则:布置于该工序成形 工作区域及易发生面品问题区域;受力区域也需均 匀布置,如图10所示。
合理设置压料器的压料面积,确保凸模接触制 件的区域和压料区域能有效压料,一般翼子板成形 工序③未完全翻边到位,工序④此处保留70 mm宽 压料面积,其余位置背空,如图11所示。 工序③、④斜楔分界线不能重合,以确保不出 现压痕或产生棱线不顺问题,工序④镶件边界线需 靠近A柱角部(注意负角),但至少过工序③相交线 最小10 mm,如图12所示。
2.5 加工策略分析
影响机理:为实现棱线的突出效果,一般对工 序③的翻边凸模圆角会实施做尖处理,导致工序④ 和工序③形状不一样,存在间隙,受力时使尖角产 生包裹在工序④圆角的变形趋势,且制件边缘长短 不同,导致板料受到拉力不同,最终不同的拉力使R 角变形不一致,导致棱线不顺,如图13所示。
改进方案:将工序④凸模圆角做尖,消除材料 变形空间,抑制其变形,同时在制件设计阶段尽量 减小边缘长短差异,过渡区域适当加长,如图 14 所示。
2.6 模具装配调试分析
影响机理:模具装配滑车拼接缝处间隙不合 理、型面研合不均匀,导致整体棱线基准存在差错, 影响制件棱线光顺。 改进方案:依据尺寸链组成,影响装配精度有 以下因素,X方向:侧向滑配、中心滑配,如图15 (a) 所示;Y方向:滑车限位状态;Z方向:压板滑配、盖板 滑配、模座滑配、防侧导板滑配,如图 15(b)所示。
最终装配效果需保证凸模盖板与凸模滑车分缝间 隙≤0.01 mm。
除保证模具装配精度以外,同时须确保门轴侧 压料力、翻边间隙合理性。压料芯底部氮气缸压力 确定后可视为一个定量值,在一定的压力下,钳工 须保证研合面积及研合效果,如表1所示。
3 结束语
关于翼子板门轴侧棱线不顺的问题,首先在制 件结构分析阶段要对造型细节进行确认,确保在良 好的造型结构下,通过工艺方案、模具结构的设计 进行问题预防,并结合模具零件精细化加工、装配、 研合等各环节相互协调,最终才能保证预期的品质 效果。
▍原文作者:张 宇, 赵晓柏
▍作者单位:长城汽车股份有限公司