前围是车身前部与车舱分隔模块,而前围流水槽零件则是前围模块最主要的结构之一。它的主要作用是通过零件自身沟槽的特殊结构将前窗流下的雨水排出车身,避免因雨水流进车身内部引起锈蚀问题。另外,它还在一定程度上传递来自车身前减振器的载荷。因此前围流水槽在与车身其他零件搭接时,其配合间隙及位置精度等尤为重要。
前围流水槽零件本身形状并不复杂,因排水需要,其主体结构呈“U”字形。但因其料厚薄,回弹难以控制,且装配要求较高,在实际装车调试阶段难度较大,调试到合格产品件消耗时间多。不同的车型前围流水槽的结构也不尽相同,一般分为分体式与整体式结构,整体式结构比较常见,可节约模具的开发成本,而分体式前围流水槽调试难度相对较低。本文主要基于整体式前围流水槽结构进行分析,并简单介绍分体式前围流水槽的调试特点。
产品结构图1为三种前围流水槽的结构形式,(a)(b)为整体式结构,(c)为分体式结构(零件A和B),即减振器安装孔(图1(a)2位置)与侧面的立壁面(图1(a)1位置,与通风盖板搭接)不在同一个零件上,中间通过焊接搭接在一起。
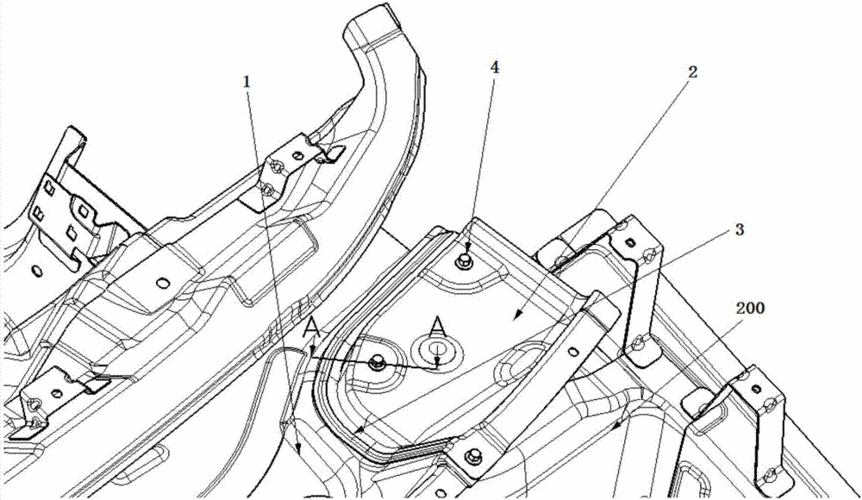
图1 前围流水槽两种结构
工艺设计图1中的三种前围流水槽的材质料厚分别为 B170P1-0.8mm、H180YD+ZF45/45-0.7mm、H220YD+ZF45/45-0.8mm,各材质的性能参数见表1。
表1 各材质的性能参数
因零件尺寸较大,翻边的位置及孔的数量较多,整体式前围流水槽基本为5序模具完成,如图3所示。主要工序内容为:拉延→修边+冲孔→侧修边+冲孔→翻边+整形→冲孔+侧冲孔。分体式则是由两个零件搭接而成,因此需要增加一个零件模具工装开发。
图2 前围流水槽分总成结构
图3 整体式前围流水槽工序内容
工艺设计阶段,考虑到零件底部平面起伏较大,普通拉延方式可能会造成起皱缺陷。为确保前围流水槽底平面的质量,模具在第一序拉延模上做双活设计,即在上模设计压料芯结构,压住局部板料再成形。经CAE模拟分析后,如图4所示,零件局部可能存在一定回弹,因此需在回弹区域做适当回弹补偿,减少回弹量。
图4 某车型整体式前围流水槽回弹分析结果
装车问题点整体式前围流水槽在调试期间的主要问题在于单件自由状态翻边面回弹,即减振器安装孔所在面与立壁翻边面的角度相对于数模增大,而分总成的定位孔在立壁翻边面的法兰边上,导致减振器安装孔向-X方向偏移(图5)。另一方面,零件料厚较薄在焊接后易受焊接精度的影响,存在不稳定性。
图6是一个分体式前围流水槽带立壁翻边的零件,零件A工序内容与整体式前围流水槽基本相同,但因减振器安装孔与立壁翻边面不在同一个零件,在翻边回弹的情况下,可以通过调整零件B与其搭接的止口边,向中间靠近,可作为一个改善偏孔的手段,减少调试的难度。
图5 前围流水槽分总成在检具上的状态及偏孔方向
图6 分体式前围流水槽装配
结论针对前围流水槽单件及分总成的回弹、偏孔等问题,经过现场多轮调试,主要措施分以下几方面。
⑴调整模具的翻边间隙,提升模具研合率,尽可能保证冲压单件的精度及稳定性,减小回弹量。
⑵采用立式工位器具(图7),不叠放,减小存放及转运过程中的变形。
图7 前围流水槽工位器具
⑶在减振器安装孔上增加辅助定位销,过定位约束X方向的相对位置。
⑷针对已出现的调试难点形成总结,在产品件设计阶段考虑调试的方便性,综合考虑开发成本的情况下,尽可能从设计源头降低后期装车困难。
—— 来源:《锻造与冲压》2020年第4期