根据行业通用标准,外板件的A面(外观面)区域模拟阶段合格的评判标准:最小减薄率≥3%,主应变≥0.03,次应变≥0,外板区域次应力≥1.1倍材料屈服强度,用100mm长度油石打磨划线时面品参数范围±0.03mm。由于零件造型和工艺限制等原因,难以实现上述所有参数都达到标准。当上述参数没有全部达到标准时,现场零件大概率会出现断线缺陷。以某翼子板为例进行成形参数检查,结果如图3~图7所示,该翼子板的材料为CR240,料厚为0.7mm,模拟材料的屈服强度为256.3MPa,即1.1倍的屈服强度为281.93MPa,取282MPa。
图3中间区域最小减薄没达到3%,结果未达标;图4中间区域主应变没达到0.03,结果未达标;图5中A面区域次应变全部大于0,结果达标;图6中A面区域全部达到282MPa,结果达标;图7中A柱有3处面品缺陷值大于0.03,结果未达标。5项检查参数中2项达标,3项因产品造型和工艺方法受限未达标,预判现场零件大概率会出现断线缺陷。
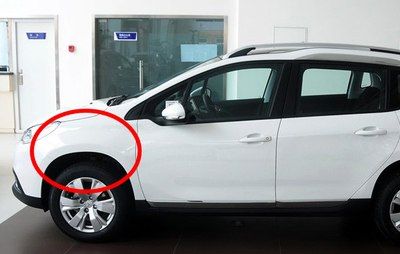
翼子板出现断线缺陷的原因是零件拉深成形不充分、修边后回弹应力释放。后工序较多出现的面品问题都是因拉深工序隐患所致,修边后隐患放大而出现缺陷。假设翼子板拉深成形后A柱圆角处相接的曲面由于凸圆角拉深后回弹变大,造成相接曲面挠曲变形,在整体回弹趋势下不同位置的回弹量不同,使此处型面造成微量扭曲,扭曲后的型面曲率如图8所示,最终在零件上表现为油石打磨断线缺陷,如图9所示。
3 提前补偿
优化翼子板A柱处断线缺陷的方法分为两步:①设计工艺补充面时,在容易发生面品缺陷处,通过调整工艺补充面使之拉深均匀、充分,从根本上减少面品缺陷的产生,具体方法主要有增大拉深深度、设置工艺反坎增加拉深筋深度等,如图10所示;②当工艺补充面无法使面品参数都符合标准时,设计NC加工数据时在容易发生面品缺陷处进行型面补偿,且全工序的上、下模都要设计补偿,具体方式如图11所示。虚线是原始型面,实线是向下补偿0.1mm后的型面,补偿范围通常取30~50mm,具体范围值根据模拟结果中缺陷的位置和范围以及结合以往项目的现场经验来综合考虑,补偿与不补偿交界处保证曲率连续。该翼子板补偿范围选取的是40mm,向下补偿0.1mm,全工序的上模和下模都进行补偿。
做完补偿后的面、曲率在某种状态下会发生变化,主要决定因素是零件A面原始曲率的方向。当型面原始曲率向下时,补偿后的曲率会出现反向,如图12和图13所示;当型面原始曲率向上时,补偿后的曲率不会反向,仅曲率梳高度出现变化,如图14和图15所示。补偿与不补偿交界处要保证曲率连续,补偿后的曲率出现反向时,不是突变而是均匀变化,整段曲率仍然光顺。所以补偿后的型面无论曲率是否反向,只要是曲率仍保持光顺过渡,即可认为合格。
4 项目验证
理论研究需要经过实际验证才能证明其准确性,项目1翼子板的理论分析显示面品(surfacelows)不达标,如果前期不进行补偿处理,现场大概率会出现断线缺陷。制作NC加工数据时,在翼子板A柱容易发生面品缺陷处做40mm宽的向下补偿,补偿量为0.1mm,同时检查曲率的连续性和斑马纹的光顺性,确认没有问题后,将全工序的上、下模NC加工面都进行了替换补偿,之后进行模具零件加工、装配和调试。对零件首次出件进行面品缺陷检查,翼子板A柱未出现明显的断线,油石划线检测如图16所示。
为验证方案的通用性,选取了4个项目的翼子板进行油石打磨断线补偿验证,理论分析时均出现了面品主要参数不达标的情况,故以这些项目进行验证。制作NC加工数据时,在翼子板A柱容易发生面品缺陷处进行与项目1相同的补偿处理,之后进行模具零件加工、装配和调试。模具首次出件时进行面品缺陷检查,4个项目的翼子板A柱均没有出现明显的断线,验证结果统计如表1所示,表明零件前期模拟的缺陷风险位置在NC加工数据上提前补偿,可以优化甚至消除断线缺陷。
▍原文作者:陈磊